Why is my ice maker not working? This frustrating question plagues many homeowners and businesses when they discover their once-reliable ice maker suddenly stops working. Ice makers are more and more popular in modern kitchens and commercial environments, making their unexpected failure particularly frustrating, especially when the warranty coverage is expired.
Most ice maker failures come from several common issues in its normal operation. Water supply problems—including insufficient pressure, blocked lines, or faulty inlet valves—are usually the first thing I checked. Then, you can look for mechanical component malfunctions involving compressors, ejection systems, or sensor which stop the ice maker working. If you don’t know how to clean an ice maker, I guess the mineral buildup is another typical culprit.
This comprehensive guide will help you pinpoint the problems why your ice maker not working, and hopefully it’s simple enough troubleshoot. With enough information, I want my readers to determine when professional service becomes necessary. But I must warn you first, most of the time, an ice maker not working means you need a real service.
I’ve made a comprehensive “Ice Maker FAQ” series collecting all common ice maker problems to help Ice Artisan readers quickly troubleshoot their ice maker units.
- ⚖️ Countertop vs undercounter ice makers
- 👍 Are portable ice makers worth it?
- ⚡ How much electricity does an ice maker use?
- 💧 Does an ice maker use a lot of water?
- 🪣 Do ice makers need to be drained?
- 🚫 Can ice makers cause water damage?
- 🚰 Do ice makers need water lines?
- 🔊 Are countertop ice makers loud?
- 😭 Do ice makers make a lot of noise?
- 🔗 Are countertop ice makers safe?
- ⛺ Can ice makers be used outdoors?
- 🔌 Can ice makers be left running all the time?
- 🚗 Can ice makers be used in RV?
- 🗄️ Can ice makers be installed in cabinets?
- ❄️ Do portable ice makers keep ice frozen?
- 🛠️ Can ice makers be used in garages?
- 📄 Do ice makers store ice?
- 💡 How does ice maker work?
- 🎰 How does a commercial ice maker work?
- 🛠️ How to install an undercounter ice maker?
- ❄️ How to make clear ice in ice maker?
- 🪣 How to increase ice production in ice maker?
- ⏳ How long does an ice maker take to make ice?
- 🔗 When to replace ice maker filter?
- ⏱️ When to replace ice maker?
- 💡 How to clean ice maker?
- 😭 Why does my ice maker smell bad?
- 🫗 How to drain an ice maker?
- 🪣 How to unclog an ice maker?
- 🔗 How do I unstick my ice maker arm?
- 💧 How to fix ice maker leaking water?
- ❄️ Why is my portable ice maker making too much ice?
- 🥵 Why is my ice maker hot?
- 🔌 What happens if you don’t turn off the ice maker?
Ice Artisan‘s best picks
Why is my ice maker not working?
An ice makers typically stop working due to water supply issues, clogged filters, sensor malfunctions, mineral buildup, or electronic control failures. You need to examine each causes of ice maker not working, and the process is not very simple.
If you can turn on the ice maker, but ice maker doesn’t produce ices, you should read my article of How to fix ice maker not making ice?
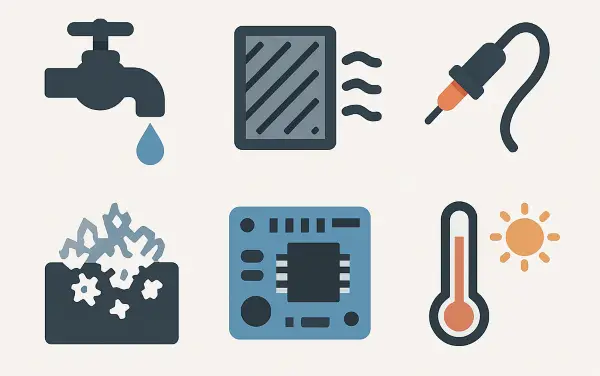
So what causes ice maker to stop working? Below are some possible reasons:
- Water supply issues are the main cause of ice maker not working. Every ice maker needs a consistent water flow to function properly. For undercounter ice makers, you need to check for compressed water lines, especially under narrow counters where the line may get pinched against the wall.
For portable ice maker, it often display specific error codes when water levels in the reservoir are too low for proper operation. - Clogged filters is another reason to prevent normal ice production. Most ice makers include water filters to remove impurities and improve ice quality. These filters gradually collect mineral deposits that restrict water flow over time. Many users don’t follow the manufacturer’s recommended filter replacement schedule, as a result the performance deteriorates until the ice maker stops working completely.
- Temperature sensor failures frequently cause ice maker malfunctions. Ice makers rely on many precise temperature sensors. When these sensors fail, the ice maker may incorrectly measure freezing conditions, either stopping production too early or failing to start the freezing cycle at all. The combination of moisture and temperature changes particularly damages these sensitive electronic parts.
- Mineral buildup inside critical components presents a widespread problem, particularly in hard water areas. Calcium and magnesium deposits gradually block ice makers, and ice molds can interfere with normal function. This buildup causes slowly decreasing ice production before eventually not working.
- Control board problems can disable your ice maker from working. This electronic board is how we humans speak with our ice makers. Voltage fluctuations, moisture exposure, or component failure can damage this control board, thus block our only communication with the ice maker. Look for symptoms like inconsistent operation, unresponsive buttons, or error codes specific to your ice maker model.
- Ambient temperature issues significantly impact ice production efficiency. Many users place their ice makers in locations unsuitable for optimal performance. Most units specify acceptable operating temperature ranges (typically 50-90°F) outside of which production decreases or stops completely. Ice makers in cold garages often have no ice production, while outdoor units may struggle during extreme summer heat.
- Harvest cycle malfunctions is another common issue. The ejection mechanism—whether using heating elements to release ice or mechanical arms to remove it from molds—can be blocked or damaged. Ice cubes then create blockages, making the ice maker fail to properly release new ice cubes.
- Power supply problems, though not popular, can be a cause for your ice maker not working. Beside obvious issues like unplugged units or tripped circuit breakers, other undetected electrical problems can affect performance. Voltage inconsistencies from overloaded circuits typically show minimal symptoms like reduced ice production. It is mostly the problem for an old ice maker.
- Sealed system deficiencies usually appear in older units or those that have been physically damaged. The sealed cooling system may develop leaks, reducing freezing capacity. I found it mainly happens when you’re buying a secondhand ice maker unit.
How to fix my ice maker not working?
Knowing all the possible causes for your ice maker not working, we will try to troubleshoot and try to make the ice maker great again:
1, Water supply issues
When your ice maker stops working because of the water supply—check that the supply valve is fully open and inspect the entire water line for kinks or compression points. For undercounter ice makers, examine the water line of the ice maker from the wall connection to the appliance. Test water pressure by disconnecting the line and running water into a container—you should see a steady, strong flow. For portable units, simply fill the reservoir to the indicated level using filtered water at room temperature.

2, Filter issues
Normally, you need a filter replacement after 3-6 months depending on usage and water quality. When replacing filters, purge your ice maker by discarding the first several batches of ice, which may contain residual carbon particles or accumulated impurities. Consider installing pre-filtration systems in areas with particularly hard water to improve filter longevity. Know when to replace ice maker filter can help you avoid this issue. If you don’t want to replace the filter, you can check this guide on “How to unclog an ice maker?”, which can help you save a few dollars.
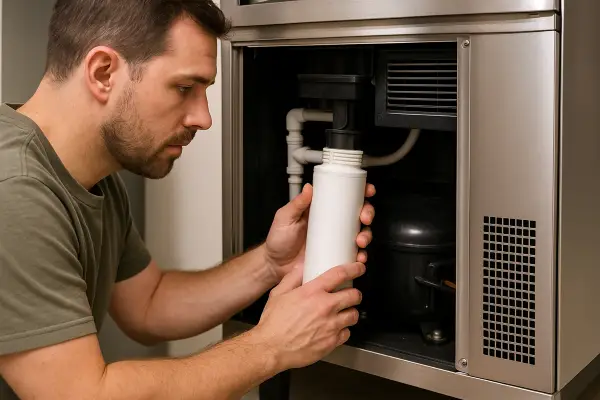
3, Sensor issues
Read the manual, find your ice maker’s reset button, then reset the whole ice maker system. If sensor issues still happen, perhaps you will need a technician ice maker. Undercounter ice makers’ sensors are quite easy to replace, but only do it if you know what you’re doing. I write an article of How to replace ice maker sensor for commercial ice makers, make sure you follow this guide.
4, Mineral buildup issue
If you regularly clean your ice maker, this won’t be an issue. However, if you follow my step-by-step guide to clean your ice maker, it can fix the mineral buildup issue. Simply create a cleaning solution using food-grade vinegar or manufacturer-approved cleaner, then use it in the water source of the ice maker, then turn the machine on. Regular cleanup significantly clean the mineral buildup, thus maintain optimal performance.

5, Control board issues
Sadly, if you have doubt that the problem is involving your ice maker’s control board, you must ask an ice maker technician to help you. Swapping mainboard or replace capacitors are not just plug and play, so unless you’re willing to take the risk, just find your nearest ice maker repairing service.
6, Ambient temperature issues
Try not to operate your ice maker outside the temperature range, that’s simple. If you’re using an outdoor ice maker, you can put it in shadow to save it from direct summer heat. Make sure you don’t block the front ventilation of your ice maker. Consider some seasonal adjustments—increasing thermostat settings during winter months for garage ice makers, or cover them to avoid summer’s sunlight.
7, Harvest cycle malfunctions
Another issue that you must ask for an ice maker service, and this time, it could be very costly to fix the issue. For units with mechanical harvesting systems, the technician needs to inspect arms and ejectors for proper alignment and function. In the heating ejector, you can try some lubrication first. Check my article to know how do I unstick my ice maker arm.
8, Power supply problems
It mainly happens to commercial ice makers, and you should find a power conditioning equipment to stabilize the utility fluctuations that can damage sensitive electronic ice machines.
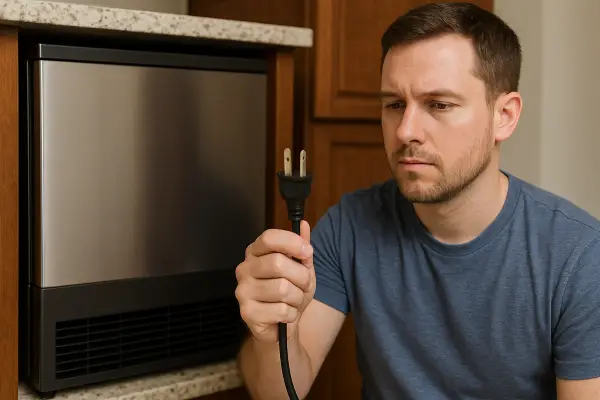
9, Sealed system deficiencies
Again, call your nearest ice maker service.
Conclusion
Troubleshooting an ice maker that has stopped working requires a systematic approach. Start with the most common issues: water supply, filter condition, and electrical connections and follow my guide to see which one you can fix, and which one you shouldn’t touch. Know when to call professionals. Cooling system problems typically require specialized tools and technicians to fix properly.