How to fix ice maker not making ice is a common problem that frustrates many homeowners and business owners alike. You’ve likely experienced it yourself – your ice maker appears to be running normally with all lights on, yet the ice bin remains empty. This issue affects everyone from families preparing for parties to restaurant owners serving customers who need cold drinks.
After fixing lots of ice makers in homes and businesses, I’ve found that when an ice maker runs but produces no ice, several issues might be responsible. Unlike when the ice maker not working, these problems are narrowed less, and most of the time, you can fix it yourself without calling for a professional.
First thing first, we need to indicate the problem that blocks your ice maker produce ices. After that, just follow my guide, and I’m sure everyone can enjoy iced drinks very soon.
I’ve made a comprehensive “Ice Maker FAQ” series collecting all common ice maker problems to help Ice Artisan readers quickly troubleshoot their ice maker units.
- βοΈ Countertop vs undercounter ice makers
- π Are portable ice makers worth it?
- β‘ How much electricity does an ice maker use?
- π§ Does an ice maker use a lot of water?
- πͺ£ Do ice makers need to be drained?
- π« Can ice makers cause water damage?
- π° Do ice makers need water lines?
- π Are countertop ice makers loud?
- π Do ice makers make a lot of noise?
- π Are countertop ice makers safe?
- βΊ Can ice makers be used outdoors?
- π Can ice makers be left running all the time?
- π Can ice makers be used in RV?
- ποΈ Can ice makers be installed in cabinets?
- βοΈ Do portable ice makers keep ice frozen?
- π οΈ Can ice makers be used in garages?
- π Do ice makers store ice?
- π‘ How does ice maker work?
- π° How does a commercial ice maker work?
- π οΈ How to install an undercounter ice maker?
- βοΈ How to make clear ice in ice maker?
- πͺ£ How to increase ice production in ice maker?
- β³ How long does an ice maker take to make ice?
- π When to replace ice maker filter?
- β±οΈ When to replace ice maker?
- π‘ How to clean ice maker?
- π Why does my ice maker smell bad?
- π« How to drain an ice maker?
- πͺ£ How to unclog an ice maker?
- π How do I unstick my ice maker arm?
- π§ How to fix ice maker leaking water?
- βοΈ Why is my portable ice maker making too much ice?
- π₯΅ Why is my ice maker hot?
- π What happens if you don’t turn off the ice maker?
Ice Artisan‘s best picks
How to fix an ice maker not making ice?
To fix an ice maker not making ice, you need to check the water supply first, then inspect for clogged filters or mineral buildup that might be blocking water flow, and don’t forget to install a power conditioner for your commercial ice maker unit.
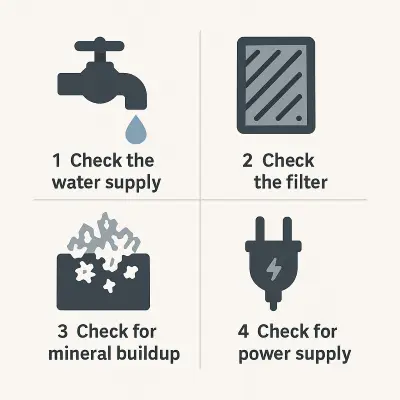
1, Check the water supply
When your ice maker runs but doesn’t make ice, water-related problems are usually to blame. First, check your water supply valve β it may have been closed accidentally (dumb as it may sound, but it happens a lot). Follow the water line of the ice maker from the main supply to your ice maker and make sure the valve is fully open. If your ice maker shares a water line with other appliances, low water pressure could be the issue. For commercial ice makers, installing a dedicated water line with a pressure gauge often solves this problem. Check my guide on “How to install an undercounter ice maker?” to know how to make perfect installation for your commercial ice maker.

2, Check the filter
Clogged filters are another common culprit. Most ice makers have a water filter that trap sediment, chlorine, and minerals. These filters gradually become blockages, reducing water flow and stop your ice maker making ice. Replace filters every 3-6 months, or more often if you have hard water. Many ice makers have a simple auto-clean feature, so make sure you use this feature often. For countertop ice makers, I recommend to use filtered water to keep the ice maker last longer. You should know when to replace ice maker filter.
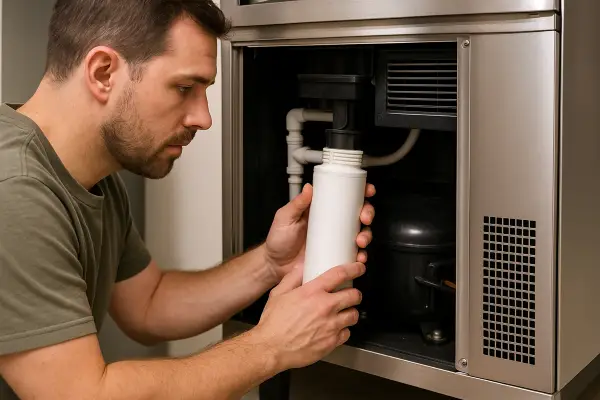
3, Check for mineral buildup
Most of the time we can stop at replacing the filter, but sometimes, yes, sometimes the situation is worse. Calcium deposits collect on heating elements, water distribution systems, and evaporator plates, essentially choking the ice-making process. When replacing the filter but you don’t find your ice maker start making ice, you should think of this possibility. You will need to clean your ice maker, by making a special combination of vinegar, or just use the manufacturer-approved cleaner, then let your ice maker run again. Soon, it will declutter all the minerals inside your ice maker system.
After that, purge the ice maker by discarding 2-3 next batches of ice production. Here is a simple guide on how to unclog an ice maker, if things don’t get better.
4, Check for power supply
Like other high power-consumption appliances, the commercial ice maker often needs a power conditioner to improve the quality of the power that is delivered to this machine. Even when it doesn’t fix your ice maker not making ice, you still need one installed for your commercial ice maker.
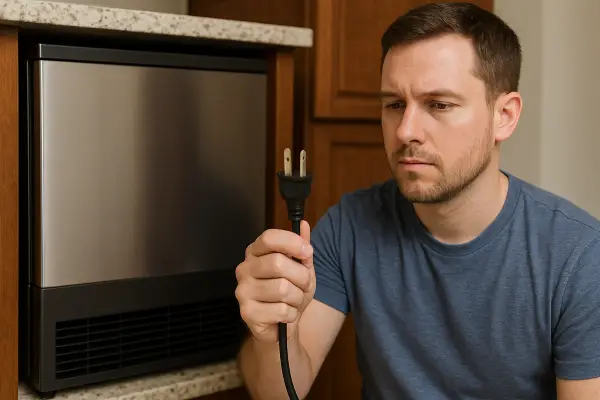
Conclusion
Successfully fixing ice maker issues requires a step-by-step approach combined with some basic knowledge. Most problems can be solved through careful troubleshooting, from simple water valve adjustments to more complex refrigerant system checks.
Understanding how your ice maker works gives you the power to make effective repairs. Regular maintenance prevents most breakdowns, while quick action reduces downtime and saves money on professional repairs.
Remember that different ice types need different troubleshooting approaches. Bullet, nugget, crescent, and clear ice makers each have unique systems, so avoid applying one-size-fits-all solutions.
When your ice maker runs but makes no ice, the answer is usually found in easily overlooked details. Check for clogged filters, mineral buildup, or environmental factors before assuming there’s a major mechanical failure.
With these troubleshooting techniques and regular maintenance habits, you can get your ice maker working again. A little patience and proper diagnosis will ensure your family, customers, or business operations aren’t left without ice when you need it.